Hunting Energy Services (HES), Subsea Technologies Division, is a manufacturer of subsea hydraulic products for the oil and gas industry. Their suite of hydraulic valve products includes applications for drilling control, production control, and Intervention Workover Control Systems (IWOCS).
As part of their commitment to excellence in manufacturing, HES uses SAE standard AS4059 to assure the cleanliness of testing and flushing fluids to improve the overall quality of their equipment. While adherence to this standard is not mandatory, it is accepted and often demanded by their customers. This in turn helps ensure that their products function properly to avoid costly malfunctions during subsea operation.
Particle Analysis Challenges
There are times during qualification testing when HES would intentionally contaminate test fluids with extreme levels of ISO 12103-1 Test Dust, per customer requirements, to see if valves or couplings would malfunction. During one of the qualification tests, they sent out fluid samples for testing at a local lab using laser diffraction technology. When they received the results back from the outside lab, they were not convinced that the data was entirely correct. They suspected that the laser diffraction analysis was missing some of the larger particles.
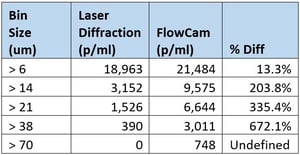
HES then decided to use the FlowCam with its particle imaging technology. They were curious to know how the laser diffraction results compared to the FlowCam results. For example, with laser diffraction, no particles were recorded >65 µm, while with the FlowCam, particles were detected at that size range and even >100 µm.
The technology used in laser diffraction (like other non-imaging technologies) converts all particles to an equivalent spherical diameter (ESD). In certain cases, long fibers would be counted as small spheres. And in other cases, translucent particles were missed entirely. Laser diffraction is not a reliable source for registering and sizing particles with a low aspect ratio. HES realized that the technique they had been using was vastly undercounting particles and missing many others.
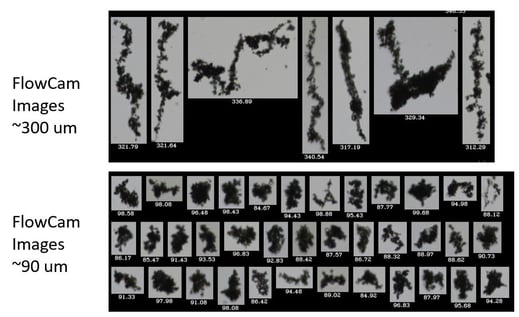
Their outsourced technique of laser diffraction could not differentiate between solids, fibers, and air bubbles. Additionally, this technique required considerable dilution, rates up to 100:1 to function properly. The FlowCam could run the sample without any dilution.
One of the advantages of using the FlowCam is that HES could implement size bin filters to count and categorize particles of different sizes in conjunction with the AS4059 requirements.
The FlowCam was able to immediately provide count data for particles in each of the size bins. Additionally, they could create a filter to recognize and exclude air bubbles in the wash water that would skew the particle count unnecessarily.
Based on Chart 1A, laser diffraction revealed 0 particles above 70 µm in size. Without images to back up the data, those who rely solely upon laser diffraction may never know what they miss.
![]() |
Chart 1A. Customer’s Laser Diffraction Results Chart 1B. FlowCam Result |
The Advantages of Flow Imaging
FlowCam particle imaging provides a more accurate analysis of the particles because it is a direct measurement technology. It does not make any assumptions about the spherical shape of any particle, nor does it make any indirect measurements of any particle based upon shadows, diffraction, or reflection. In addition, all particles can be verified directly since all particles can be viewed individually. Therefore, FlowCam particle imaging is a more trustworthy particle measurement technology for use in mission critical particle cleanliness applications.